ERP Software Affects GMP Compliance
January 9, 2013
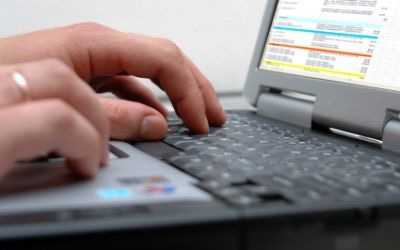
Manufacturers of dietary supplements are being increasingly challenged, by regulatory bodies and the public alike, to improve their manufacturing processes and deliver safe, high-quality products. Yet, according to FDA, violations have been found in more than half of the dietary supplement facilities it has inspected in the past four years. With cGMP (current good manufacturing practice) regulations now in effect for all dietary supplement manufacturers, the pressure to comply or die" is crucial to the survival and growth of the industry.
The proper Enterprise Resource Planning (ERP) software solution can have a significant impact on ensuring quality products are delivered to customers and compliance with cGMP regulations are met with efficiency and ease. Unfortunately, an ill-fitting ERP solution can have the opposite effect.
With hundreds of ERP systems on the market, how do you select the best-fit solution to ensure your processes meet FDA's stringent requirements?
When selecting an ERP system, look first for a solution with built-in features specifically for your industry, in addition to the traditional ERP functionalities. An ERP system that can handle the formulation through shipment process in a single system with no bolt-ons or customizations will be able to provide greater process control than one with multiple programs, systems and bridges built between software modules. The premise is simple; the software that requires the most customization will be the one most vulnerable to process instability.
From a functionality standpoint, an ERP solution that can handle batch tickets, formula management, quality control (QC) testing, lot tracking, document management and regulatory reporting within a single system will be a best-fit solution for highly regulated process manufacturers. If any of these elements are built on top of," customized or bolted to an existing ERP solution instead of being built natively into the code, there is a risk that workarounds will be developed that hinder the process control needed to maintain GMP compliance.
Batch Tickets
The best-fit ERP solution for GMP compliance will be able to provide and archive individual batch tickets to govern the production process. The tickets should include sign off and QC tests for each phase of production ensuring the strictest QC. In cases of FDA audit, the archived batch tickets will provide a well-documented trail of process control.
Formula Management
To ensure compliance, users of the ERP software need to be able to track revisions to formulas, understand by individual batch exactly how a product was made, monitor any changes in quality, quantity and location, and provide an audit trail throughout the revisions. When formula management is native to the ERP solution, it should provide all of this functionality and ensure that changes made to formulas immediately impact inventory, production requirements and planning throughout the manufacturing process. A solution that can also dynamically scale those formulas will provide added functionality and efficiencies in meeting current demand levels, optimizing ingredient usage and tracking all ingredient costs.
QC Testing
The best-fit ERP solution should have the ability to set up user-defined QC tests to manage how often QC tests are performed, what is testedwhether it is a group of items from a specific vendor, multiple lots of items or individual ingredientsand what amounts are tested. The system should automatically put lots in inventory on quality hold until the testing results are entered into the system, preventing failed items from entering the manufacturing process. Incremental testing of inventory ensures quality over time.
For process manufacturers who must employ rigorous lot tracking capability, these QC functionalities are game-changers. They greatly improve ingredient traceability throughout the supply chain and throughout a given products life cycle. With the right ERP solution, there are virtually no barriers to implementing additional tracking steps, thus improving visibility when problems do occur.
Lot Tracking and Recall
A Warehouse Management System (WMS) designed directly into the ERP system, when used correctly, is one of the few tools available that can both reduce operating costs and improve process control. WMS should allow users to instantly track changes and view inventory status through multiple facilities, providing users transaction processing with tight controls on lot tracking. Using bar-code technology, scanners should be able to update the ERP system at any stage of the process, greatly reducing the chance of warehouse errors while improving productivity. In the case of a recall, the system should be able to provide users with a Bill of Materials implosion and explosion to show all the raw material lots that comprise the finished good or in which finished goods a raw material lot was used. This level of visibility provides manufacturers the capability to quickly and efficiently recall items, recalling only the affected lots.
Document Management and Regulatory Reporting
The best-fit ERP solution will allow you to manage documents from archiving standard operating procedures (SOPs) to providing proper shipping documentation by batch, customer or product. The ERP solution should have the flexibility to handle a wide range of regulatory reporting requirements and provide certificates of analysis (CoAs) and other documents quickly and easily at the point of shipment.
Ensuring a quality product through a reliable and repeatable process takes strict and rigorous control of that process. The right ERP system will provide the process control needed to ensure quality and compliance in a highly scrutinized and highly regulated industry.
Jay Deakins is founder and president of Deacom Inc., Wayne, PA. Deacom Inc. is the producer of DEACOM, a complete Enterprise Resource Planning (ERP) system for process manufacturers with difficult-to-handle requirements. Prior to establishing Deacom Inc., Deakins founded and served as president of The Sun and Earth Company, a manufacturer of all-natural cleaning products distributed through national supermarket chains and other mass merchants.
About the Author(s)
You May Also Like