Keep Dateline NBC from Knocking at Your Door
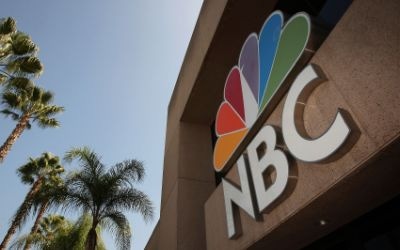
A recent story by Dateline NBC put a negative spotlight on the dietary supplement industry by uncovering potential problems with third-party analytical laboratories. This is just one example that shows why qualifying all contract facilities used by dietary supplement manufacturers, including, and particularly, third-party laboratories, is important. In fact, the role that verification testing plays in cGMP (current good manufacturing practice) compliance, to ensure products meet their specifications and are free from contaminants, cannot be minimized.
Under the FDA dietary supplement cGMP rule, companies must establish specifications for dietary ingredients, finished dietary supplements and well as other components. They must then verify that every specification has been met, usually by some form of examination or testing. Due to a lack of internal capabilities and/or capacity, most dietary supplement manufacturers will use third-party labs to perform at least some verification testing. Companies also will use contract labs to confirm information on certificates of analysis (CoAs) is accurate as part of qualifying ingredient suppliers. In this capacity, the lab becomes an extension of the companys quality systems; therefore, the lab and the work they perform must comply with cGMPs.
Much has been written about the cGMP requirements to establish and verify specifications, but so far, the industry has skirted around the challenges involved with meeting requirements for adequate lab operations. This includes: the role of quality control (QA) in lab operations; cGMP compliance within the lab; GMP-related documentation; the issues surrounding appropriate sampling, methodology, reference standards, etc.; and how to appropriately deal with out-of-specification results. These challenges can be magnified when working with third-party laboratories. In fact, FDA considers lab operations so important that the cGMP Rule has a specific subpart devoted solely to lab operations: 21 CFR 111 Subpart J Production and Process Control Systems Requirements for Laboratory Operations.
If a company is going to use a third-party lab to perform some or all of its testing, why does it need to know about the cGMP requirements for lab operations? Isnt the requirement under the rule met with the testing results? The answer is no. It is the dietary supplement manufacturer and label holders responsibility to ensure the finished product has been produced in compliance with the cGMPs, and that includes testing and laboratory operations. Inaccurate results and/or a failure in lab cGMP compliance could result in adulteration of the finished dietary supplement. In these circumstances, companies may find themselves in the unfortunate situation of issuing product recalls or dealing with FDA enforcement.
Qualifying a third-party lab is similar to qualifying any other supplier or contract manufacturer; laboratories must be qualified according to internal company procedures, and documentation of this process must be maintained. The goal is to evaluate the facility, personnel and operations to determine if it meets minimum GMP compliance and has the capabilities to perform the necessary work. This is best accomplished through on-site audits. A checklist completed by the lab, accompanied by supporting documentation, may be an adequate option, but there are basic questions that need to be answered when evaluating a lab, including:
Does the facility have adequate space for instrumentation and operations?
How are samples handled and stored?
How long does it keep samples after testing is performed?
Does it have appropriate and adequate standard operating procedures (SOPs) for all lab operations?
How are lab personnel qualified, including the lab supervisor?
Are required GMP records and documentation maintained?
Will it share documentation with its customers?
Does it have the capability to do the required testing? Verify the equipment, materials, standards, etc., exist to perform the required analyses.
Does it use analytical methods that are scientifically valid?
Does it have the expertise to develop or modify existing methodology for your needs?
Are standard reference materials used?
How are appropriate sampling plans determined?
Does it have the capacity to meet the needed volume?
What is its typical turnaround time?
How will it provide results?
Will it provide access to raw test data as well as actual results, and review raw analytical data and check calculations?
How does it handle out-of-specification results?
Third-party lab assessment also should include challenging the test results, at least occasionally, by submitting "dummy" or "check" samples for analysis and sending identical samples to another laboratory to confirm results are accurate. This is standard best practices to ensure the lab performs testing and report the actual results, instead of providing a fabricated report with expected results.
Third-party laboratories have areas of specialty and no lab is the best choice for everything. Once labs have been chosen, it's best to establish written agreements that spell out expectations on both sides.
Cara Welch, Ph.D., vice president, scientific and regulatory affairs, Natural Products Association (NPA), oversees NPA's quality assurance programs, including the NPA Natural Seal and GMP Certification for dietary supplements.
About the Author(s)
You May Also Like