Best Practices in Ingredient and Supplier Qualification
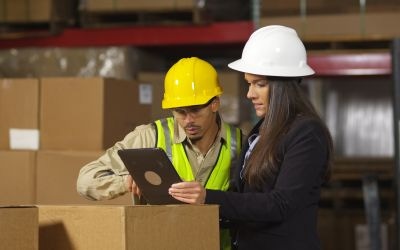
High-quality products begin with high-quality ingredients. Acquisition of these ingredients requires a system that includes setting appropriate specifications, controlling the supply chain and establishing appropriate good manufacturing practice (GMP) controls to protect and maintain ingredient quality.
Its best to start with established specificationsknowing what you are looking for prior to starting the search for the ingredient. The concept is if you know your end product and the claims youll make, you can better determine what you need to source. Here are a few tips:
Establish quality specifications for raw materials based on finished product specifications (and product claims) before sourcing materials.
Include specifications for all relevant physical, chemical and microbial parameters, as well as regulatory specifications for identity, purity, strength and composition.
Understand the manufacturing processes and set specifications that take into account the characteristics of the raw material necessary for the manufacturability of the finished product.
Determine what adulterants/contaminants may be inherent to a particular component and set limits for any that could reasonably be expected to be found in the raw material.
Beware of ingredients that are poorly characterizede.g., lack scientifically valid test methods to verify specifications or lack solid science to support safety and product claims.
Avoid making sourcing decisions based on price alone.
A robust supply chain isnt just dependent on quality ingredients; it also requires quality suppliers. To find these quality suppliers, it is important to develop a supplier qualification program. Here are some first steps:
Establish an effective internal organization for evaluating suppliers
Must include purchasing, quality, research and development (R&D), and, ideally, production/manufacturing,
Consider basing supplier qualification program on total quality management principles, including the principle of defect prevention rather than defect detection.
The qualification program should be used with all existing suppliers, as well as part of initial negotiations with new suppliers.
Qualification must be ingredient and vendor specific. A company cant include all items supplied by a given vendor unless it qualifies each ingredient.
Consider the nature and source of the component; the suppliers compliance history; how the component will be used in finished product formulations; the component stability (physical, microbial and chemical); and the component compatibility and safety.
Is the supplier meeting the regulatory requirements for the ingredient?
Review each suppliers capabilities, service performance and quality history.
Can the supplier provide quality materials that consistently meet established specifications?
Recognize the suppliers you are working with may not be the entire supply chain for the raw material(s), and expect that the supplier will provide the name and location of the manufacturer when different from the supplier.
Determine the source for the data on the certificate of analysis (CoA).
Is the testing done in-house or by contract laboratory?
Work with the supplier to determine how the material was tested and the appropriate verification testing.
Verify the reliability of the CoA by testing/examining a minimum of three to five incoming lots of the particular ingredient for all established specificationsif possible, use the same method as the supplier for best comparison.
Supplier must provide current information about product, specifications, processes, etc., on a periodic basis.
Audit your suppliers to assess their quality management systems, manufacturing, storing, warehousing and distribution practices.
While third-party certification programs can provide a measure of assurance, auditing your own suppliers allows you access to their operations and the ability to look closely at how materials of interest to you are sourced, processed and tested.
Consider supplier qualification an ongoing process versus an event, and continue to audit and re-qualify suppliers and ingredients on a regular basis.
The work to qualify a supplier is certainly not minor, but it is imperative for a quality system to improve relationships and build partnerships with suppliers. Once the work has gone into qualifying a supplier, a well-written supplier agreement can protect both parties. And for those suppliers youve already been working with, a re-written supplier agreement may be necessary to ensure your GMP compliance isnt in danger. Even though its a lot of work to qualify suppliers, sourcing of some ingredients can be fickle, so best practice would require qualifying more than one source for each ingredient when possible. Lastly, once you have found the right materials and qualified your supplier(s), treat your ingredients with care so they remain quality ingredients. Here are a few tips:
Require a CoA with every shipment.
Assign unique numbers to each lot to ensure traceability.
Ensure adequate space to segregate and hold materials based on their status.
Identify all materials and keep track of their status.
Ensure materials are held in an appropriate environment.
Assign expiration dates and rotate appropriately.
Do not use materials until all verification testing is complete and quality has approved and released the materials for use.
Managing ingredients and supply chain ensures the quality of finished products. Following current best practices, such as these, can help a company achieve efficient and effective business operations while meeting its regulatory responsibilities.
Cara Welch, Ph.D., is the senior vice president of scientific and regulatory affairs at the Natural Products Association (NPA). She oversees NPAs quality assurance programs, including the NPA Natural Seal and GMP Certification for dietary supplements. Welch earned her doctorate degree in medicinal chemistry at Rutgers University.
Vicki Whitsitt is the scientific and regulatory affairs manager for NPA. In her position, she works with the associations self-regulatory quality assurance (QA) and regulatory education programs, and manages the NPA GMP Certification Program. In this capacity, she works closely with program advisors, third-party auditors and companies seeking NPA GMP certification.
About the Author(s)
You May Also Like